Package Testing Solutions to Validate Performance
To ensure the best packaging and help lower the total cost of logistics, it is very advantageous to be able to test packaging during the design and production process. Testing procedures that follow rigorous industry standards can determine how a particular type of packaging will perform when exposed to various real-world conditions and demands. That is why the top packaging designers work with certified package testing labs, where engineers help guarantee that you have optimal, tailor-made packaging solutions.
Package Testing Directly Impacts Cost Factors
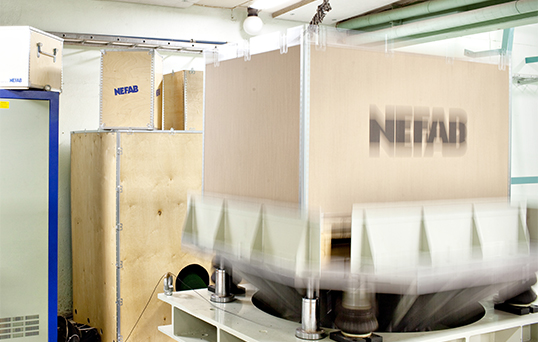
Testing the performance of a packaging design before using it to ship your products to customers offers multiple benefits. Your decisions regarding transportation methods, for example, will directly affect the choice of packaging solutions.
Ocean freight is more exposed to moisture and salt, but also subjected to general drops and shifting.
Products shipped by rail, on the other hand, are subject to specific vibrations and impacted by certain bumps and temperatures.
Truck transport will have side way impacts and compression, on top of the regular drops, bumps and climatic effects.
Regardless of what you ship or how you ship it, your products should be protected by the optimal packing solution, and one that is also the most cost effective. Before you decide to invest in a particular type of packaging and use a specific form of warehousing or transportation, you can test the packaging design and see how it will actually perform.
tests help to ensure that your packaging needs are met, based on the type of product you are packaging and the modes of transportation that will be used
Test for the Optimal Packaging Solution
Packaging is exposed to various types of stress while being filled, moved, stored, and transported. But there are several methods used to test packaging products, and there are specific tests that can be applied to a particular design or material being used. These tests help to ensure that your packaging needs are met, based on the type of product you are packaging and the modes of transportation that will be used to deliver it to your customers.
There are two main stress points in packaging:
Mechanical Strains - The most common mechanical strains on transported goods are force stresses, such as stacking pressure, impact shocks, vibrations, and drops.
Climatic Stresses - Climate plays a vital part for the durability and performance of packaging, particularly during warehousing and transportation.
Fortunately, there are test designs to evaluate the performance of packaging, regardless of how it may be exposed to these kinds of stresses and strains.
Package Testing Under Specific Conditions
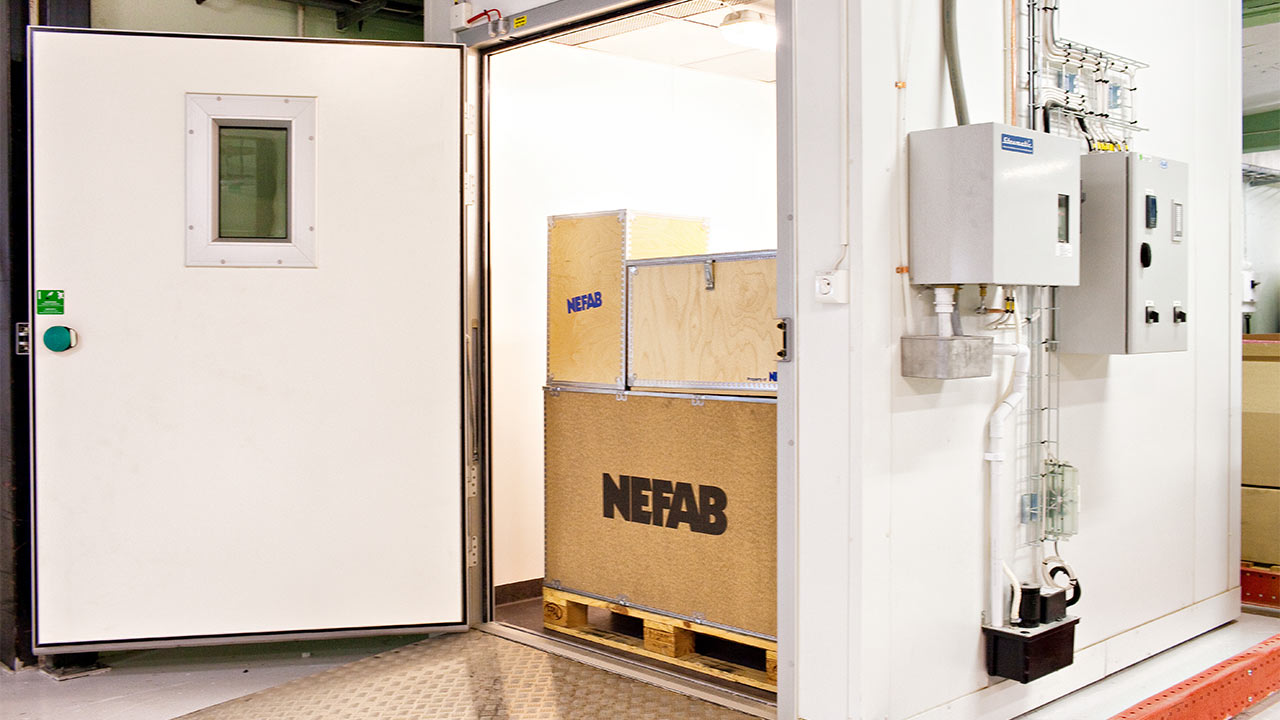
Even when a packaging solution is too impractical to test in the conventional ways, computer analysis can perform the tests
Many packaging stresses and strains can be accurately tested, including these:
Compression/Stacking performance is tested by applying and releasing pressure, and by applying and maintaining pressure.
Vibration can be tested horizontally, vertically, or on a multi-axis – and the amount of vibration can also be calibrated to test for degrees of vibration intensity.
Shock tests can be performed in a number of ways, including free falls, rotational shock, shocks applied to hazardous materials packaging, incline shocks, drops, and more.
Temperature and atmospheric stress tests can include various degrees of humidity and temperature cycles.
Other tests include water spraying and testing of corrugated packaging materials and designs.
Additional Testing Capabilities
Packaging designers with access to a certified packaging design lab can test a wide variety of packaging performance characteristics, including these:
Rolling and Toppling
Bending
Moisture Absorption
Cutting Strength
Glue Joints
Sheet/Steel Material
Edge Crushing
Bursting Strength
Compression Strength
ESD Testing
Corrosion Evaluations
Puncture Resistance
Plus Much, Much More…
Computer-Aided FEA Analysis
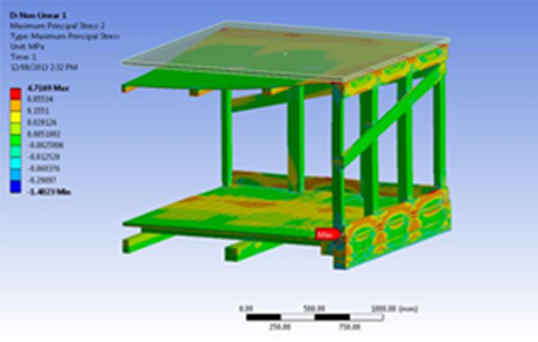
Even when a packaging solution is too impractical to test in the conventional ways, computer analysis can perform the tests. FEA (Finite Element Analysis) is a computerized testing tool engineers can use in a virtual environment, to test for optimized packaging solutions such as these:
Cost Take-Out: FEA provides insight on areas of a design that may be replaced with a cheaper material or different shape without compromising performance and integrity.
Risk Analysis: FEA can help determine if the solution complies with hazardous material packaging requirements and is safe and secure for transportation of dangerous products.
Extremely Large/Heavy Packaging: Some industrial packaging is too large or heavy to test in a conventional way, but it can be accurately and thoroughly tested using FEA technology.
Vertical Compression Simulation: FEA also enables testing of packaging – such as extremely large and heavy crates – that would be impractical or too expensive to test using traditional methods.
Prototyping: Designs can be performance tested using FEA before creating prototypes, to save you time and money.
ISTA Testing Standards
The International Safe Transit Association (ISTA) sets industry standards and guidelines for testing of packaging. The world’s best packaging designers work with ISTA-certified packaging testing labs, to ensure superior packaging performance and to facilitate tailor-made packaging design solutions. Each type of ISTA test has a unique set of strict guidelines and laboratory equipment requirements that must be adhered to in the packaging laboratory. There are multiple categories of tests under ISTA guidelines, depending on how extensively one wants to simulate the transport.
ISTA Testing Protocol
Test protocols are also grouped into what ISTA calls a Series. Testing moves from non-simulation of transport environmental hazards through simulation in general or broad terms – and finally to a test developed from a comprehensive collection of field data. These testing procedures are numerous, but here are three examples of common packaging solution tests:
ISTA Procedure 1A: Under the protocols for ISTA Procedure 1A, which applies to packaged products weighting 150 lb (68 kg) or less, fixed displacement vibration and shock testing is performed.
ISTA Procedure 2A: ISTA Procedure 2A, which applies to the same weight category, tests atmospheric conditioning, compression, fixed displacement or random vibration, and shock testing.
ISTA Procedure 3A: ISTA Procedure 3A applies to packaged products for parcel delivery system shipments of 70kg (150 lb) or less. This particular procedure is a general simulation test for individual packaged products, and is appropriate for four different package types commonly distributed as individual packages, either by air or ground. The types include standard, small, flat and elongated packages. Tests are conducted on atmospheric pre-conditioning, random vibration with and without top load, and shock.
Nefab Testing Labs and Packaging Solutions
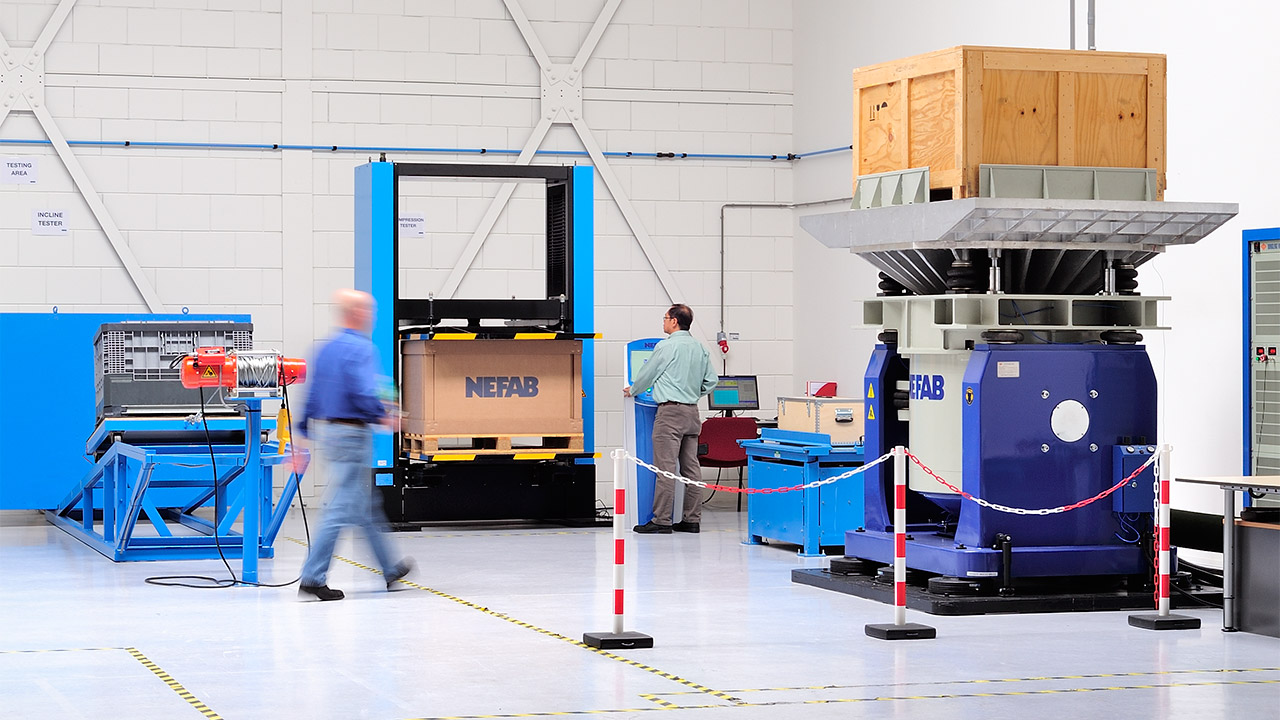
That’s why Nefab tests designs in order to find the ideally-balanced solution.
Nefab operates certified, ISTA-compliant testing labs around the world. Engineers in these labs put all of Nefab's designs and products through rigorous testing, and can also perform many other standards or customized tests, based on specific products and stress factors. We are familiar with and can test according to standards like ETSI, NEBS, IEC, ISO, ASTM, and many others.
Nefab also recognizes that there is no need to overpay for packaging that is more secure than necessary. That's why Nefab tests designs in order to find the ideally-balanced solution. We consult and collaborate with each of our customers, and perform appropriate tests, to deliver the best packaging solutions for product safety as well as total cost of logistics.
The main difference, compared to many other testing labs, is that Nefab's are run by designers and engineers who can help improve packaging instead of just testing it. That kind of proactive approach helps ensure that you deliver products without damage, spillage, unwanted delays, regulatory complications, or other issues. Plus it helps control the total cost of logistics, for both you and your customer, while preserving your valuable reputation.